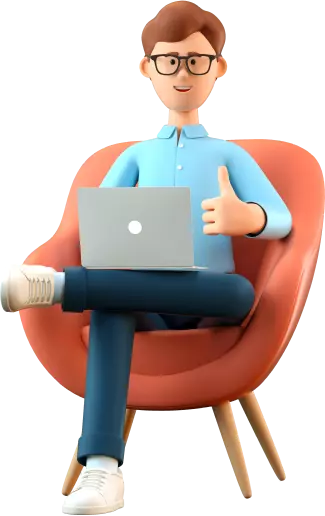
на первый
заказ
Дипломная работа на тему: Испытание твёрдость по Бринеллю
Купить за 600 руб.Введение
1. Опишите систему понятий, входящих в понятие "марка материала"Материаловедением называют прикладную науку о связи состава, строения и свойств материалов. Решение важнейших технических проблем, связанных с экономией материалов, уменьшением массы машин и приборов, повышением точности, надежности и работоспособности механизмов и приборов во многом зависит от развития материаловедения.
Теоретической основой материаловедения являются соответствующие разделы физики и химии, однако наука о материалах в основном развивается экспериментальным путем.
Напряжение - величина нагрузки, отнесенная к единице площади поперечного сечения испытуемого образца.
Деформация - изменение формы и размеров твердого тела под влиянием приложенных внешних сил. Различают деформации растяжения (сжатия), изгиба, кручения, среза. В действительности материал может подвергаться одному или нескольким видам деформации одновременно.
Прочность - способность материала сопротивляться разрушению под действием нагрузок. Оценивается пределом прочности и пределом текучести. Важным показателем прочности материала является также удельная прочность - отношение предела прочности материала к его плотности.
Упругость - способность материала восстанавливать первоначальную форму и размеры после прекращения действия нагрузки. Оценивают пределом пропорциональности и пределом упругости.
Пластичность - способность материала принимать новую форму и размеры под действием внешних сил, не разрушаясь при этом. Характеризуется относительным удлинением и относительным сужением.
2. Сформулируйте принципы обозначения стандартных марок легированных сталей по ГОСТ4543 и в иностранных стандартах
Принципы маркировки сталей в России
В России принята буквенно-цифровая система маркировки легированных сталей. Каждая марка стали содержит определенное сочетание букв и цифр. Первые две цифры показывают содержание углерода в сотых долях процента. Легирующие элементы обозначаются буквами русского алфавита: Х - хром, Н - никель, В - вольфрам, М - молибден, Ф - ванадий, Т - титан, Ю - алюминий, Д - медь, Г - марганец, С - кремний, К - кобальт, Ц - цирконий, Р - бор, Ц - ниобий. Буква А в середине марки стали показывает содержание азота, а в конце марки - то, что сталь высококачественная. Цифры после каждой буквы обозначают примерное содержание соответствующего элемента, однако при содержании легирующего элемента менее 1,5% цифра после соответствующей буквы не ставится.
Маркировка сталей в Германии.
Национальный стандарт Германии DIN (Deutsche Industrienorm) осуществляет маркировку сталей двумя способами.
Первый способ - с помощью цифр, обозначающих номер материала. Первая цифра характеризует способ производства стали. Вторая цифра характеризует особенности обработки стали.
Второй способ - обозначение с помощью букв и цифр. Этот вид предусматривает обозначение сталей по степени легирования и виду термической обработки.
Особенности маркировки сталей в стандартах США.
В соответствии с национальными стандартами ASTM (American Society for Testing and Materials) и SAE (Society Automotive Engineers) в США принята цифровая система маркировки конструкционных сталей, в которую в некоторых случаях добавляют буквы. Большинство сталей, за исключением коррозионностойких и жаростойких, маркируется четырехзначным числом. Первая цифра указывает основной легирующий элемент, вторая - его содержание в процентах, третья и четвертая соответствуют содержанию углерода в сотых долях процента. Первая цифра 1 принята для обозначения углеродистых сталей, в этом случае вторая цифра - 0. Например, сталь по ASTM-SAE марки 1015 соответствует стали марки 15 по российскому стандарту, а 1045 - марке 45.
Первая цифра 2 соответствует сталям легированным Ni, цифра 3 - Ni и Сr; 4 - Мо, Мо и Сr, Мо, Сr и Ni; 5 - Сr; 6 - Сr и V; 7 - Сr и W; 8 - Ni, Сr и Мо; 9 - также Ni, Сr и Мо.
Таким образом сталь марки 5140 по ASTM-SAE соответствует российской стали марки 40Х, а сталь 8625, легированная Ni-Сr-Мо, содержит, %: 0,23-0,28 С; 0,4-0,7 Ni; 0,4-0,6 Сr; 0,15-0,25 Мо; 0,15-0,35 Si; 0,7-0,9 Мn; 0,035 Р; 0,040 S.
Если сталь должна обеспечивать необходимую прокаливаемость, то после цифр ставится буква Н, например 8625Н.
Россия
США
20Х
5120, 5120Н
35ХМ
4135, 4135Н
40ХН2МА
3. Дайте расшифровку стандартных марок сталей по варианту задания, назовите структурный класс и примерное назначение
12ХГДАФ - сталь конструкционная легированная качественная.
Примерное назначение: лист, проволока, трубы, лента, детали работающие при умеренных напряжениях.
38ХНЗВА - сталь конструкционная легированная высококачественная.
Примерное назначение: валы, оси, шестерни и другие крупные особо ответственные детали.
4Х5МФ1С - сталь инструментальная штамповая.
Примерное назначение: пресс-формы для литья под давлением цинковых, алюминиевых и магниевых сплавов, молотовые и прессовые вставки (толщиной или диаметром до 200-250 мм), при горячем деформировании конструкционных сталей, инструмент для высадки заготовок из легированных конструкционных и жаропрочных материалов на горизонтально-ковочных машинах.
10Х13Л - сталь конструкционная легированная качественная, для отливок, коррозионно-стойкая.
Примерное назначение: различные детали, работающие при температуре до 400°С. Сталь коррозионно-стойкая, не стойкая в сернистых газах.
Таблица 1 Химический состав сталей
Сталь
Химический элемент %
С
Сr
Мо
Мn
Сu
Р
12ХГДАФ
38ХНЗВА
4Х5МФ1С
10Х13Л
4. Что необходимо понимать под термином "КАЧЕСТВО СТАЛИ"?
Качество стали определяется содержанием вредных примесей. Основные вредные примеси - это сера и фосфор. Так же к вредным примесям относятся газы (азот, кислород, водород).
Сера - вредная примесь - попадает в сталь главным образом с исходным сырьём - чугуном. Сера нерастворима в железе, она образует с ним соединение FeS - сульфид железа. при взаимодействием с железом образуется эвтектика ( Fе + FeS ) с температурой плавления 9880 С. Поэтому при нагреве стальных заготовок для пластической деформации выше 9000 С сталь становится хрупкой. При горячей пластической деформации заготовка разрушается. Это явление называется красноломкостью. Одним из способов уменьшения влияния серы является введение марганца. Соединение Mns плавится при 1620°С, эти включения пластичны и не вызывают красноломкости. Содержание серы в сталях допускается не более 0.06%.
Фосфор - попадает в сталь главным образом также с исходным чугуном, используемым также для выплавки стали. До 1.2% фосфор растворяется в феррите, уменьшая его пластичность. Фосфор обладает большой склонностью к ликвации, поэтому даже при незначительном среднем количестве фосфора в отливке всегда могут образоваться участки, богатые фосфором. Расположенный вблизи границ фосфор повышает температуру перехода в хрупкое состояние (хладноломкость). Поэтому фосфор, как и сера, является вредной примесью, содержание его в углеродистой стали допускается до 0.050%.
5. Приведите основные характеристики механических свойств стали, по которым оцениваются стали конкретного назначения
Почти все стали материал конструкционный и в широком смысле слова: включая стали для строительных сооружений, деталей машин, упругих элементов, инструмента и для особых условий работы - теплостойкие, нержавеющие, и т.п. его главные качества:
- прочность (способность выдерживать при работе достаточные напряжения)
- пластичность (способность выдерживать достаточные деформации без разрушения, как при производстве конструкций, так и в местах перегрузок при их эксплуатации), вязкость (способность поглощать работу внешних сил, препятствуя распространению трещин).
Для каждого назначения выбирают сталь и ее состояние с оптимальным сочетанием прочности и пластичности.
Трубы для паропроводов. На всех электростанциях пар при температуре 530...575°С и давлении 14...25,5 МПа (260ат) подается от котла к турбине по толстостенным (60 мм при диаметре 325 мм) бесшовным горячекатаным трубам. Труба паропровода за 100000 ч работы (11 лет) может раздуться не более, чем на 1% (далее возможна катастрофа). Столь медленную ползучесть обеспечивает только одна теплостойкая сталь - во всем мире это 12Х1МФ или 15Х1М1Ф. Для термической обработки (нормализации и высокого отпуска) нужна однородная прокаливаемость (ферритные пятна резко снижают долговечность). Трещины ползучести развиваются по границам зерна, с участием годами накапливающихся здесь сегрегации фосфора (а также олова и сурьмы). Поэтому целесообразно применение особо чистой - первородной шихты.
Стальная проволока. При диаметре 1 мм и менее стандарты разных стран гарантируют для холоднотянутой патентированной пружинной проволоки предел прочности σв > 2500...2900 МПа, для канатной σв > 1300...2400 МПа. Автомобильные шины высокого качества армированы прядями кордной проволоки с σв до 4500 МПа при диаметре около 0,1мм. Внутри высокопрочного, предварительно напряженного железобетона натянута арматурная проволока с σв > 1400...1900 МПа при диаметре 3...12мм.
При такой прочности проволоке нужен и запас пластичности: нити каната должны выдерживать перегибы и удары. Этот запас проверяется испытаниями: на многократный "гиб с перегибом", скручивание, навивку, разрыв с узлом. Необходимая структура - тонко пластинчатый перлит (сорбит), упрочняемый холодным волочением. Чтобы выдерживать при этом большие обжатия, нужна эвтектоидная сталь - углеродистая сталь 65...85.
6. Как и для чего нужно управлять количеством и качеством не металлических включений?
Постоянные примеси в стали: марганец, кремний, сера, фосфор, а также газы: кислород, азот, водород.
Марганец - полезная примесь; вводится в сталь для раскисления и остается в ней в количестве 0,3-0,8%. Марганец уменьшает вредное влияние кислорода и серы.
Кремний - полезная примесь; вводится в сталь в качестве активного раскислителя и остается в ней в количестве до 0,4%, оказывая упрочняющее действие.
Сера - вредная примесь, вызывающая красноломкость стали - хрупкость при горячей обработке давлением. В стали она находится в виде сульфидов. Красноломкость связана с наличием сульфидов FeS, которые образуют с железом эвтектику, отличающуюся низкой температурой плавления (988 °С) и располагающуюся по границам зерен. При горячей деформации границы зерен оплавляются, и сталь хрупко разрушается. От красноломкости сталь предохраняет марганец, который связывает серу в сульфиды MnS, исключающие образование легкоплавкой эвтектики. Устраняя красноломкость, сульфиды MnS, так же как и другие неметаллические включения (оксиды, нитриды и т. п.), служат концентраторами напряжений, снижают пластичность и вязкость стали. Содержание серы в стали строго ограничивают. Положительное влияние серы проявляется лишь в улучшении обрабатываемости резанием.
Фосфор - вредная примесь. Он растворяется в феррите, упрочняет его, но вызывает хладноломкость-снижение вязкости по мере понижения температуры. Сильное охрупчивающее действие фосфора выражается в повышении порога хладноломкости. Каждая 0,01 % Р повышает порог хладноломкости на 25 °С. Хрупкость стали, вызываемая фосфором, тем выше, чем больше в ней углерода. Фосфор - крайне нежелательная примесь в конструкционных сталях. Однако современные методы выплавки и переплавки не обеспечивают его полного удаления. Основной путь его снижения - повышение качества шихты.
Кислород, азот и водород - вредные скрытые примеси. Их влияние наиболее сильно проявляется в снижении пластичности и повышении склонности стали к хрупкому разрушению. Кислород и азот растворяются в феррите в ничтожно малом количестве и загрязняют сталь неметаллическими включениями (оксидами, нитридами). Кислородные включения вызывают красно- и хладноломкость, снижают прочность. Повышенное содержание азота вызывает деформационное старение. Атомы азота в холоднодеформированной стали скапливаются на дислокациях, образуя атмосферы Коттрелла, которые блокируют дислокации. Сталь упрочняется, становится малопластичной. Старение особенно нежелательно для листовой стали (≤0,1%С), предназначенной для холодной штамповки. Последствия старения-разрывы при штамповке или образование на поверхности полос скольжения, затрудняющих ее отделку.
Водород находится в твердом растворе или скапливается в порах и на дислокациях. Хрупкость, обусловленная водородом, проявляется тем резче, чем выше прочность материала и меньше его растворимость в кристаллической решетке. Наиболее сильное охрупчивание наблюдается в закаленных сталях с мартенситной структурой и отсутствует в аустенитных сталях. Повышенное содержание водорода в стали при ее выплавке может приводить к флокенам. Флокенами называют внутренние надрывы, образующиеся в результате высоких давлений, которые развивает водород, выделяющийся при охлаждении в поры вследствие понижения растворимости. Флокены в изломе имеют вид белых пятен, а на поверхности мелких трещин. Этот дефект обычно встречается в крупных поковках хромистых и хромоникелевых сталей. Для его предупреждения стали после горячей деформации медленно охлаждают или длительно выдерживают при температуре 250 °С. При этих условиях водород, имеющий большую скорость диффузии, не скапливается в порах, а удаляется из стали. Наводороживание и охрупчивание стали возможны при травлении в кислотах, нанесении гальванических покрытий и работе в водородсодержащих газовых средах.
Случайные примеси - элементы, попадающие в сталь из вторичного сырья или руд отдельных месторождений. Сталь, выплавленная из уральских руд, содержит медь, из керченских - мышьяк. Случайные примеси в большинстве случаев оказывают отрицательное влияние на вязкость и пластичность стали.
7. На какие свойства стали разного назначения влияет величина зерна?
Размер зерна влияет на свойства стали, особенно на вязкость, которая значительно выше у металлов с мелким зерном.
Внутри зерна феррита нет сильных препятствий скольжению. Поэтому сопротивление его деформации течения создают границы зерна, и чем мельче зерно феррита, тем выше предел текучести. Чем больше деформация, тем больше препятствий создают внутри зерна сами следы скольжения и тем меньше влияет размер зерна на сопротивление течению. Поэтому предел прочности σв зависит от размера зерна феррита слабее, чем предел текучести σт. Если потребитель использует сталь "в состоянии поставки", характеристикой стали может быть величина зерна феррита. Но если сталь будет термически обрабатываться, то важно "наследственное зерно аустенита", которое получится после нагрева под закалку до стандартной для этой стали температуры. У мартенсита столь сложная субзеренная структура, что в ней границы зерна исходного аустенита - препятствие пренебрежимо слабое. Прочность мартенсита от величины зерна не зависит. Перлит, сорбит, бейнит - двухфазные структуры. Их прочность определяется прежде всего температурой образования (дисперсностью цементита), а не величиной зерна исходного аустенита.
Мелкое зерно желательно при всех структурах, если есть риск хрупкого разрушения. Поэтому в высококачественных легированных конструкционных сталях наследственное зерно аустенита должно быть не крупнее 5-6-го балла.
8. Как управлять величиной зерна?
Величина зерен зависит от числа центров кристаллизации и скорости роста кристаллов. Чем больше центров кристаллизации, тем мельче зерно металла. Величина зерен, образующихся при кристаллизации, зависит от количества самопроизвольно зарождающихся центров кристаллизации и от количества нерастворимых примесей, всегда имеющихся в жидком металле.
Изменить число центров и размер зерна можно четырьмя методами:
- изменить скорость охлаждения и тем самым величину переохлаждения;
- увеличить или уменьшить перегрев металла перед разливкой;
- ввести в жидкий металл мельчайшие нерастворимые примеси;
- уменьшить путем добавки активных растворимых примесей поверхностное натяжение.
При небольшой степени переохлаждения (малой скорости охлаждения) будет получено крупное зерно. С увеличением степени переохлаждения размер зерна в затвердевшем металле уменьшается.
Последние два метода осуществляются при модификации введением специальных добавок. Ими являются оксиды (например, AI2O3), нитриды, сульфиды и другие соединения. Такие нерастворимые примеси являются готовыми центрами кристаллизации. Центрами кристаллизации в данном металле или сплаве могут быть только такие твердые частицы, которые по размеру соизмеримы с атомами основного металла. Кристаллическая решетка таких твердых частиц должна быть близка по своему строению и параметрам решетке кристаллизующегося металла. Чем больше таких частиц, тем мельче будут зерна закристаллизовавшегося металла. Чем выше скорость охлаждения, тем больше возникает центров кристаллизации и, следовательно, мельче зерно металла.
9. Что подразумевается под оптимальной структурой?
Основными компонентами, из которых состоят стали и чугуны, являются железо и углерод.
По структуре стали бывают:
- доэвтектоидные (феррит + перлит)
- эвтектоидные (перлит)
- заэвтектоидные (перлит + цементит)
Рисунок 1 Диаграмма состояния железо-цементит
Диаграмма состояния железо-цементит. Ж-жидкость; Ц-цементит (индексы: 1- первичный II-вторичный; III- третичный); А-аустенит; Ф-феррит; П-перлит (эвтектоид, т.е. механическая смесь феррита и цементита); Л-ледебурит (эвтектика, т.е. механическая смесь аустенита и цементита) Линия ACD - ликвидус, линия AECF - солидус. СD - линия первичного цементита (из жидкого расплава); SЕ- линия вторичного цементита (при перекристаллизации аустенита) РQ- линия третичного цементита (из феррит а).
10. Опишите процесс закалки стали
Закалка - термическая операция, состоящая в нагреве закаленного сплава выше температуры превращения с последующим достаточно быстрым охлаждением для получения структурно неустойчивого состояния сплава. Для сталей различают закалку до - и заэвтектоидных сталей. В структуре закаленной стали преобладает мартенсит. Мартенсит имеет высокую твердость и низкую вязкость, как конструкционный материал не используется. Для доэвтектоидных сталей температура закалки должна быть на 30 - 50 град. выше Ас3, а для заэвтектоидных - на 30 - 50 град. выше Ас1. При закалке доэвтектоидной стали с температуры выше Ас1, но ниже Ас3 в структуре наряду с мартенситом сохраняется часть феррита, который снижает твердость в закаленном состоянии и ухудшает механические свойства после отпуска. Такая закалка называется неполной. Для заэвтектоидных сталей оптимальная температура закалки лежит в интервале между Ас1 и Ас3 и теоретически является неполной. Здесь наряду с мартенситом закалки сохраняется часть оставшегося цементита, наличие которого полезно. Нагрев выше Ас3 приводит к вредным перегреву и обезуглероживанию стали. Закалка бывает объемной (под закалку нагревают насквозь все изделие) и поверхностной (осуществляют местный, чаще поверхностный нагрев).
В зависимости от формы изделия, марки стали и нужного комплекса свойств применяют различные способы охлаждения:
Закалка в одном охладителе. Нагретую до нужной температуры деталь переносят в охладитель и полностью охлаждают. В качестве охлаждающей среды используют: воду - для крупных изделий из углеродистых сталей; масло - для небольших деталей простой формы из углеродистых сталей и изделий из легированных сталей. Основной недостаток - значительные закалочные напряжения.
Закалка в двух средах или прерывистая. Нагретое изделие предварительно охлаждают в более резком охладителе (вода) до температуры ~ 300°С и затем переносят в более мягкий охладитель (масло). Прерывистая закалка обеспечивает максимальное приближение к оптимальному режиму охлаждения. Применяется в основном для закалки инструментов. Недостаток: сложность определения момента переноса изделия из одной среды в другую.
Ступенчатая закалка. Нагретое до требуемой температуры изделие помещают в охлаждающую среду, температура которой на 30 - 50°С выше точки МН и выдерживают в течении времени, необходимого для выравнивания температуры по всему сечению. Время изотермической выдержки не превышает периода устойчивости аустенита при заданной температуре. В качестве охлаждающей среды используют расплавленные соли или металлы. После изотермической выдержки деталь охлаждают с невысокой скоростью. Способ используется для мелких и средних изделий.
Изотермическая закалка. Отличается от ступенчатой закалки продолжительностью выдержки при температуре выше МН, в области промежуточного превращения. Изотермическая выдержка обеспечивает полное превращение переохлажденного аустенита в бейнит. При промежуточном превращении легированных сталей кроме бейнита в структуре сохраняется аустенит остаточный. Образовавшаяся структура характеризуется сочетанием высокой прочности, пластичности и вязкости. Вместе с этим снижается деформация из-за закалочных напряжений, уменьшаются и фазовые напряжения. В качестве охлаждающей среды используют расплавленные соли и щелочи.
Закалка с самоотпуском. Нагретые изделия помещают в охлаждающую среду и выдерживают до неполного охлаждения. После извлечения изделия, его поверхностные слои повторно нагреваются за счет внутренней теплоты до требуемой температуры, то есть осуществляется самоотпуск. Применяется для изделий, которые должны сочетать высокую твердость на поверхности и высокую вязкость в сердцевине (инструменты ударного действия: молотки, зубила).
11. Как управлять типом структуры, образующейся при закалке
Основными параметрами являются температура нагрева и скорость охлаждения.
По температуре нагрева различают виды закалки:
Полная, с температурой нагрева на 30…50°С выше критической температуры Ас3. Применяют ее для доэвтектоидных сталей. Изменения структуры стали при нагреве и охлаждении происходят по схеме: Неполная закалка доэвтектоидных сталей недопустима, так как в структуре остается мягкий феррит.
Неполная с температурой нагрева на 30…50 °С выше критической температуры Ас1. Применяется для заэвтектоидных сталей. Изменения структуры стали при нагреве и охлаждении происходят по схеме: После охлаждения в структуре остается вторичный цементит, который повышает твердость и износостойкость режущего инструмента. После полной закалки заэвтектоидных сталей получают дефектную структуру грубоигольчатого мартенсита. Заэвтектоидные стали перед закалкой обязательно подвергают отжигу - сфероидизации, чтобы цементит имел зернистую форму.
Охлаждение при закалке.
Для получения требуемой структуры изделия охлаждают с различной скоростью, которая в большой степени определяется охлаждающей средой, формой изделия и теплопроводностью стали.
Режим охлаждения должен обеспечить необходимую глубину закаленного слоя. При высоких скоростях охлаждения при закалке возникают внутренние напряжения, которые могут привести к короблению и растрескиванию.
Очень медленное охлаждение может привести к частичному отпуску мартенсита и увеличению количества аустенита остаточного, а следовательно к снижению твердости.
В качестве охлаждающих сред при закалке используют воду при различных температурах, технические масла, растворы солей и щелочей, расплавленные металлы.
12. Опишите понятия "закаливаемость" и "прокаливаемость"
Закаливаемость и прокаливаемость - важнейшие характеристики сталей.
Закаливаемость - способность стали приобретать высокую твердость при закалке.
Закаливаемость определяется твердостью поверхности закаленной детали и зависит главным образом от содержания углерода в стали. При закалке, различных деталей поверхность их, как правило, охлаждается со скоростью, большей VКр, следовательно, на поверхности образуется мартенсит, обладающий высокой твердостью. Стали с содержанием углерода менее 0,2% не закаливаются.
При закалке любых деталей даже в самых сильных охладителях невозможно добиться одинаковой скорости охлаждения поверхности и сердцевины детали. Следовательно, если скорость охлаждения сердцевины при закалке будет меньше VKp, то деталь не прокалится насквозь, т. е. там не образуется мартенсит.
Прокаливаемостью - называют способность стали закаливаться на определенную глубину.
Условились при оценке прокаливаемости закаленными считать слои, в которых содержится не менее 50% мартенсита (полумартенситная зона).
Установлено, что легирование стали любыми элементами, кроме кобальта, увеличивает прокаливаемость, так как при этом повышается устойчивость переохлажденного аустенита.
13. Что такое "полоса прокаливаемости"? Дайте описание "полосы прокаливаемости" стали, заданной номером рисунка в варианте задания
Прокаливаемость - способность получать закаленный слой с мартенситной и троостомартенситной структурой, обладающей высокой твердостью, на определенную глубину. За глубину закаленной зоны принимают расстояние от поверхности до середины слоя, где в структуре одинаковые объемы мартенсита и троостита. С введением в сталь легирующих элементов (Сr, Ni, Мо, Мn, W, V) закаливаемость и прокаливаемость увеличиваются.
Таблица 2 Полосы прокаливаемости стали 38ХС
14. Что такое стали пониженной прокаливаемости, и для каких деталей их применяют?
Под прокаливаемостью подразумевают глубину проникновения закаленной зоны. Несквозная прокаливаемость связана с тем, что деталь быстрее охлаждается с поверхности, чем с сердцевины. С уменьшением критической скорости закалки увеличивается и глубина закаленного слоя, и если Vк будет меньше скорости охлаждения в центре, то сечение закалится на сквозь. Если сечение велико и скорость на поверхности меньше Vк, то сталь не закалится даже на поверхности. Для практической оценки прокаливаемости используют величину - критический диаметр, т.е. максимальный диаметр (размер) образца, который прокаливается насквозь в данном охладителе. Чем лучше свойства охладителя тем больше Dкр.
Для получения при закалке тонкого твердого слоя, равномерного по поверхности применяют мелкозернистые стали с пониженной прокаливаемостью, у которых ограничено содержание марганца и кремния, а также хрома, никеля, меди и пр. и создана устойчивая наследственная мелкозернистость путем модифицирования алюминием, титаном и пр. При увеличении содержания алюминия (сверх 0,10-0,12%) измельчение зерна прекращается, но так как твердый раствор продолжает обогащаться алюминием, прокаливаемость стали повышается.
Например:
В автомобильной промышленности для шестерен неответственного назначения, допускающих сквозную закалку зубьев (например, венец маховика автомобильных двигателей, работающий только при пуске), используют сталь с пониженной прокаливаемостью марки 55ПП содержащей 0,55 - 0,63%С и <0,5 % примесей (Si, Мn, Сr и Си) и регламентированной прокаливаемости 47РП, содержащей 0,44 - 0,51%С; 1,0 - 1,2 % Мn; 0,06 - 0,12%Тi.
15. Опишите процесс старения стали
Старение - термическая обработка, при которой главным процессом является распад пересыщенного твердого раствора.
В результате старения происходит изменение свойств закаленных сплавов.
В отличие от отпуска, после старения увеличиваются прочность и твердость, и уменьшается пластичность.
Старение сплавов связано с переменной растворимостью избыточной фазы, а упрочнение при старении происходит в результате дисперсионных выделений при распаде пересыщенного твердого раствора и возникающих при этом внутренних напряжений.
Основное назначение старения - повышение прочности и стабилизация свойств.
Различают старение естественное, искусственное и после пластической деформации.
После старения повышается прочность и снижается пластичность низкоуглеродистых сталей в результате дисперсных выделений в феррите цементита третичного и нитридов.
16. Перечислите требования к автомобильному листу
Основную массу производимого холоднокатаного листа составляет автомобильный лист. Кузов автомобиля изготовлен холодной штамповкой (и точечной сваркой) из тонкого (0,5...3мм) листа. Листовым сталям необходим высокий запас технологической пластичности (способности металла подвергаться горячей и холодной пластической деформации).
Технологическая пластичность зависит от химического состава стали, ее микроструктуры и контролируется параметрами механических свойств. Способность стали к вытяжке при холодной штамповке определяется концентрацией углерода. Чем она меньше, тем легче идет технологический процесс вытяжки. Для глубокой вытяжки содержание углерода в стали ограничивают 0,1%; при 0,2-0,3%С возможны только гибка и незначительная вытяжка.
Микроструктура стали должна состоять из феррита с небольшим количеством перлита. Выделение по границам зерен структурно свободного (третичного) цементита строго ограничивается во избежание разрывов при штамповке. Лучше всего деформируется сталь с мелким зерном, соответствующим 7-8 номеру по ГОСТ 5639-82. При большем размере зерна получается шероховатая поверхность в виде так называемой апельсиновой корки, при меньшем - сталь становится слишком жесткой и упругой. Также нежелательна разнозернистая структура, поскольку она способствует неравномерности деформации и образованию трещин.
Для глубокой, сложной и особосложной вытяжки используют малопрочные (σв = 280-ЗЗО МПа), высокопластичные (δ = 33-45 %) стали 05, 08, 10 всех видов раскисления. Их поставляют в виде тонкого холоднокатаного листа, подвергнутого рекристаллизационному отжигу при температуре 650-690 °С. Широко применяют кипящие стали 05кп, 08кп и 10кп. Для глубокой вытяжки чаще всего используют сталь 08кп.
Кипящая сталь из-за повышенной газонасыщенности склонна к деформационному старению. В связи с этим для холодной штамповки используют сталь, микролегированную ванадием 08Фкп (0,02-0,04%V) или алюминием 08Юкп. Ванадий и алюминий связывают примеси внедрения (азот, кислород) в прочные химические соединения и препятствуют развитию деформационного старения.
Применяются также полуспокойные и спокойные стали 08пс и 08, которые, несмотря на меньшую пластичность, обладают более высокой стабильностью свойств.
17. Как понимать термин хорошая "свариваемость стали"?
Свариваемость - способность получения сварного соединения, равнопрочного с основным металлом. Для образования качественного соединения важно предупредить возникновение в сварном шве различных дефектов: пор, непроваров и, главным образом, трещин. Характеристикой свариваемости данного металла служат количество допускаемых способов сварки и простота ее технологии.
Свариваемость стали тем выше, чем меньше в ней углерода и легирующих элементов. Влияние углерода является определяющим. Углерод расширяет интервал кристаллизации и увеличивает склонность к образованию горячих трещин, которая тем больше, чем дольше металл шва находится в жидком состоянии.
В связи с этим высокой свариваемостью обладают стали, содержащие до 0,25% С. К ним относятся углеродистые стали (БСт0, БСт1-БСт4, ВСт1-ВСт4; 0,5, 08, 10, 15, 20, 25), а также низколегированные, применяемые для изготовления различных металлоконструкций: стали для трубопроводов, мостостроения, вагоностроения, судостроения 09Г2(Д), 09Г2С, 14Г2, 15ГФ(Д), 16ГС, 17ГС и др.; стали с карбонитридным упрочнением, применяемые для мостов, металлоконструкций цехов, кранов, резервуаров 14Г2АФ(Д), 15Г2СФ(Д), 16Г2АФ и др.
Сварка всех этих сталей при толщинах до 15 мм не вызывает затруднений. Сварка таких же сталей больших толщин и в термически упрочненном состоянии требует подогрева и термической обработки.
При сварке углеродистых и низколегированных сталей, содержащих более 0,3%С, возникают затруднения из-за возможности закалки и охрупчивания околошовной зоны.
Сварка высокохромистых и хромоникелевых сталей в связи с неизбежными фазовыми превращениями в металле требует специальных технологических приемов - снижения скорости охлаждения, применения защитных атмосфер и последующей термической обработки.
18. От чего зависит контактная прочность стали?
Для того чтобы обеспечить работоспособность конкретных машин и приборов, конструкционный материал должен иметь высокую конструкционную прочность.
Конструкционной прочностью называется комплекс механических свойств, обеспечивающих надежную и длительную работу материала в условиях эксплуатации.
Требуемые характеристики механических свойств материала для конкретного изделия зависят не только от силовых факторов, но и воздействия на него рабочей среды и температуры.
Высокая прочность и долговечность конструкций при минимальной массе и наибольшей надежности достигаются технологическими, металлургическими и конструкторскими методами.
Наибольшую эффективность имеют технологические и металлургические методы, цель которых - повышение механических свойств и качества материала.
Прочность - свойство, зависящее от энергии межатомной связи, структуры и химического состава материала. Энергия межатомного взаимодействия непосредственно определяет характеристики упругих свойств (модули нормальной упругости и сдвига), а также так называемую теоретическую прочность.
Проблема повышения конструкционной прочности состоит не столько в повышении прочностных свойств, сколько в том, как при высокой прочности обеспечить высокое сопротивление вязкому разрушению, т. е. надежность материала.
В углеродистых сталях закалкой на мартенсит и низким отпуском можно получить при содержании 0,4%С σв≈2400 МПа, при 0,6%С σв≈2800 МПа. Однако при такой прочности стали хрупки, эксплуатационно ненадежны.
Заданные прочность, надежность, долговечность достигаются формированием определенного структурного состояния.
Формированию благоприятной структуры и обеспечению надежности способствуют рациональное легирование, измельчение зерна, повышение металлургического качества.
19. Назовите уровни прочности канатной стали и опишите технологию упрочнения
Канатную проволоку свивают в канаты (для судов, шахт, лифтов, кранов). При диаметре 1 мм и менее стандарты разных стран гарантируют для канатной проволоки предел прочности σв > 1300...2400 МПа.
При такой прочности проволоке нужен и запас пластичности: нити каната должны выдерживать перегибы и удары. Этот запас проверяется испытаниями: на многократный "гиб с перегибом", скручивание, навивку, разрыв с узлом. Необходимая структура - тонкопластинчатый перлит (сорбит), упрочняемый холодным волочением. Чтобы выдерживать при этом большие обжатия, нужна эвтектоидная сталь - углеродистая сталь 65...85.
Чем тоньше пластинки цементита в перлите, тем больше упрочнение. Пластинки тем тоньше, чем ниже температура распада переохлажденного аустенита. Оптимальную температуру изотермического распада надо быстро достичь (если распад начнется выше, перлит грубее) и точно выдержать (чуть ниже появятся менее пластичные игольчатые структуры - бейнит). Поэтому делается патентирование: протягиваемая проволока проходит через печь (или соляную ванну) нагрева и быстро охлаждается до температуры распада аустенита в ванне с расплавом свинца или солей. После волочения делается еще низкий отпуск для снятия напряжений.
К стали для патентирования есть ряд жестких требований
Во-первых, чистота по легирующим элементам (Сг < 0,10%; Ni < 0,15%; Сu < 0,2%), иначе изотермический распад аустенита за время пребывания в свинцовой ванне не закончится, а остаток аустенита на выходе из ванны даст хрупкий мартенсит или бейнит. Использование лома в шихте исключается.
Во-вторых, вытягиваясь при волочении, границы зерна исходного аустенита превращаются в ленты вдоль оси проволоки. Если на них были сегрегации фосфора или наночастицы AlN или MnS, проволока расслаивается по этим лентам при скручивании (или при волочении). Поэтому когда-то сталь для пружин плавили только из древесноугольного чугуна (чистого по фосфору и сере). Сегодня его заменило железо прямого восстановления.
В-третьих, важна чистота по неметаллическим включениям. Если включения деформируемы и при холодном волочении (как MnS), то из округлых в слитке они превратятся в нити макроскопической длины и субмикронной толщины, а включения - дендриты - в пучок нитей, по которым и произойдет расслой. Канаты из стали 60 с округлыми сульфидами (от введения РЗМ) выдерживали 25000 перегибов, а с длинными включениями - только 18000.
20. Назовите виды коррозионных повреждений нержавеющей стали
Коррозией - называется разрушение металлов и сплавов вследствие химического и физико-химического воздействия на них окружающей среды. При техническом проектировании серьезное внимание уделяется мероприятиям защиты от коррозии.
Различают два вида коррозии металлов: химическую и электрохимическую.
Химическая коррозия происходит при воздействии на металл или сплав сухих газов при повышенных температурах и жидких неэлектролитов (бензин, смола, масло и др.).
Оглавление
- Введение- Выводы
- Список литературы
- Приложение
Список литературы
1. Опишите систему понятий, входящих в понятие "марка материала"Материаловедением называют прикладную науку о связи состава, строения и свойств материалов. Решение важнейших технических проблем, связанных с экономией материалов, уменьшением массы машин и приборов, повышением точности, надежности и работоспособности механизмов и приборов во многом зависит от развития материаловедения.
Теоретической основой материаловедения являются соответствующие разделы физики и химии, однако наука о материалах в основном развивается экспериментальным путем.
Напряжение - величина нагрузки, отнесенная к единице площади поперечного сечения испытуемого образца.
Деформация - изменение формы и размеров твердого тела под влиянием приложенных внешних сил. Различают деформации растяжения (сжатия), изгиба, кручения, среза. В действительности материал может подвергаться одному или нескольким видам деформации одновременно.
Прочность - способность материала сопротивляться разрушению под действием нагрузок. Оценивается пределом прочности и пределом текучести. Важным показателем прочности материала является также удельная прочность - отношение предела прочности материала к его плотности.
Упругость - способность материала восстанавливать первоначальную форму и размеры после прекращения действия нагрузки. Оценивают пределом пропорциональности и пределом упругости.
Пластичность - способность материала принимать новую форму и размеры под действием внешних сил, не разрушаясь при этом. Характеризуется относительным удлинением и относительным сужением.
2. Сформулируйте принципы обозначения стандартных марок легированных сталей по ГОСТ4543 и в иностранных стандартах
Принципы маркировки сталей в России
В России принята буквенно-цифровая система маркировки легированных сталей. Каждая марка стали содержит определенное сочетание букв и цифр. Первые две цифры показывают содержание углерода в сотых долях процента. Легирующие элементы обозначаются буквами русского алфавита: Х - хром, Н - никель, В - вольфрам, М - молибден, Ф - ванадий, Т - титан, Ю - алюминий, Д - медь, Г - марганец, С - кремний, К - кобальт, Ц - цирконий, Р - бор, Ц - ниобий. Буква А в середине марки стали показывает содержание азота, а в конце марки - то, что сталь высококачественная. Цифры после каждой буквы обозначают примерное содержание соответствующего элемента, однако при содержании легирующего элемента менее 1,5% цифра после соответствующей буквы не ставится.
Маркировка сталей в Германии.
Национальный стандарт Германии DIN (Deutsche Industrienorm) осуществляет маркировку сталей двумя способами.
Первый способ - с помощью цифр, обозначающих номер материала. Первая цифра характеризует способ производства стали. Вторая цифра характеризует особенности обработки стали.
Второй способ - обозначение с помощью букв и цифр. Этот вид предусматривает обозначение сталей по степени легирования и виду термической обработки.
Особенности маркировки сталей в стандартах США.
В соответствии с национальными стандартами ASTM (American Society for Testing and Materials) и SAE (Society Automotive Engineers) в США принята цифровая система маркировки конструкционных сталей, в которую в некоторых случаях добавляют буквы. Большинство сталей, за исключением коррозионностойких и жаростойких, маркируется четырехзначным числом. Первая цифра указывает основной легирующий элемент, вторая - его содержание в процентах, третья и четвертая соответствуют содержанию углерода в сотых долях процента. Первая цифра 1 принята для обозначения углеродистых сталей, в этом случае вторая цифра - 0. Например, сталь по ASTM-SAE марки 1015 соответствует стали марки 15 по российскому стандарту, а 1045 - марке 45.
Первая цифра 2 соответствует сталям легированным Ni, цифра 3 - Ni и Сr; 4 - Мо, Мо и Сr, Мо, Сr и Ni; 5 - Сr; 6 - Сr и V; 7 - Сr и W; 8 - Ni, Сr и Мо; 9 - также Ni, Сr и Мо.
Таким образом сталь марки 5140 по ASTM-SAE соответствует российской стали марки 40Х, а сталь 8625, легированная Ni-Сr-Мо, содержит, %: 0,23-0,28 С; 0,4-0,7 Ni; 0,4-0,6 Сr; 0,15-0,25 Мо; 0,15-0,35 Si; 0,7-0,9 Мn; 0,035 Р; 0,040 S.
Если сталь должна обеспечивать необходимую прокаливаемость, то после цифр ставится буква Н, например 8625Н.
Россия
США
20Х
5120, 5120Н
35ХМ
4135, 4135Н
40ХН2МА
3. Дайте расшифровку стандартных марок сталей по варианту задания, назовите структурный класс и примерное назначение
12ХГДАФ - сталь конструкционная легированная качественная.
Примерное назначение: лист, проволока, трубы, лента, детали работающие при умеренных напряжениях.
38ХНЗВА - сталь конструкционная легированная высококачественная.
Примерное назначение: валы, оси, шестерни и другие крупные особо ответственные детали.
4Х5МФ1С - сталь инструментальная штамповая.
Примерное назначение: пресс-формы для литья под давлением цинковых, алюминиевых и магниевых сплавов, молотовые и прессовые вставки (толщиной или диаметром до 200-250 мм), при горячем деформировании конструкционных сталей, инструмент для высадки заготовок из легированных конструкционных и жаропрочных материалов на горизонтально-ковочных машинах.
10Х13Л - сталь конструкционная легированная качественная, для отливок, коррозионно-стойкая.
Примерное назначение: различные детали, работающие при температуре до 400°С. Сталь коррозионно-стойкая, не стойкая в сернистых газах.
Таблица 1 Химический состав сталей
Сталь
Химический элемент %
С
Сr
Мо
Мn
Сu
Р
12ХГДАФ
38ХНЗВА
4Х5МФ1С
10Х13Л
4. Что необходимо понимать под термином "КАЧЕСТВО СТАЛИ"?
Качество стали определяется содержанием вредных примесей. Основные вредные примеси - это сера и фосфор. Так же к вредным примесям относятся газы (азот, кислород, водород).
Сера - вредная примесь - попадает в сталь главным образом с исходным сырьём - чугуном. Сера нерастворима в железе, она образует с ним соединение FeS - сульфид железа. при взаимодействием с железом образуется эвтектика ( Fе + FeS ) с температурой плавления 9880 С. Поэтому при нагреве стальных заготовок для пластической деформации выше 9000 С сталь становится хрупкой. При горячей пластической деформации заготовка разрушается. Это явление называется красноломкостью. Одним из способов уменьшения влияния серы является введение марганца. Соединение Mns плавится при 1620°С, эти включения пластичны и не вызывают красноломкости. Содержание серы в сталях допускается не более 0.06%.
Фосфор - попадает в сталь главным образом также с исходным чугуном, используемым также для выплавки стали. До 1.2% фосфор растворяется в феррите, уменьшая его пластичность. Фосфор обладает большой склонностью к ликвации, поэтому даже при незначительном среднем количестве фосфора в отливке всегда могут образоваться участки, богатые фосфором. Расположенный вблизи границ фосфор повышает температуру перехода в хрупкое состояние (хладноломкость). Поэтому фосфор, как и сера, является вредной примесью, содержание его в углеродистой стали допускается до 0.050%.
5. Приведите основные характеристики механических свойств стали, по которым оцениваются стали конкретного назначения
Почти все стали материал конструкционный и в широком смысле слова: включая стали для строительных сооружений, деталей машин, упругих элементов, инструмента и для особых условий работы - теплостойкие, нержавеющие, и т.п. его главные качества:
- прочность (способность выдерживать при работе достаточные напряжения)
- пластичность (способность выдерживать достаточные деформации без разрушения, как при производстве конструкций, так и в местах перегрузок при их эксплуатации), вязкость (способность поглощать работу внешних сил, препятствуя распространению трещин).
Для каждого назначения выбирают сталь и ее состояние с оптимальным сочетанием прочности и пластичности.
Трубы для паропроводов. На всех электростанциях пар при температуре 530...575°С и давлении 14...25,5 МПа (260ат) подается от котла к турбине по толстостенным (60 мм при диаметре 325 мм) бесшовным горячекатаным трубам. Труба паропровода за 100000 ч работы (11 лет) может раздуться не более, чем на 1% (далее возможна катастрофа). Столь медленную ползучесть обеспечивает только одна теплостойкая сталь - во всем мире это 12Х1МФ или 15Х1М1Ф. Для термической обработки (нормализации и высокого отпуска) нужна однородная прокаливаемость (ферритные пятна резко снижают долговечность). Трещины ползучести развиваются по границам зерна, с участием годами накапливающихся здесь сегрегации фосфора (а также олова и сурьмы). Поэтому целесообразно применение особо чистой - первородной шихты.
Стальная проволока. При диаметре 1 мм и менее стандарты разных стран гарантируют для холоднотянутой патентированной пружинной проволоки предел прочности σв > 2500...2900 МПа, для канатной σв > 1300...2400 МПа. Автомобильные шины высокого качества армированы прядями кордной проволоки с σв до 4500 МПа при диаметре около 0,1мм. Внутри высокопрочного, предварительно напряженного железобетона натянута арматурная проволока с σв > 1400...1900 МПа при диаметре 3...12мм.
При такой прочности проволоке нужен и запас пластичности: нити каната должны выдерживать перегибы и удары. Этот запас проверяется испытаниями: на многократный "гиб с перегибом", скручивание, навивку, разрыв с узлом. Необходимая структура - тонко пластинчатый перлит (сорбит), упрочняемый холодным волочением. Чтобы выдерживать при этом большие обжатия, нужна эвтектоидная сталь - углеродистая сталь 65...85.
6. Как и для чего нужно управлять количеством и качеством не металлических включений?
Постоянные примеси в стали: марганец, кремний, сера, фосфор, а также газы: кислород, азот, водород.
Марганец - полезная примесь; вводится в сталь для раскисления и остается в ней в количестве 0,3-0,8%. Марганец уменьшает вредное влияние кислорода и серы.
Кремний - полезная примесь; вводится в сталь в качестве активного раскислителя и остается в ней в количестве до 0,4%, оказывая упрочняющее действие.
Сера - вредная примесь, вызывающая красноломкость стали - хрупкость при горячей обработке давлением. В стали она находится в виде сульфидов. Красноломкость связана с наличием сульфидов FeS, которые образуют с железом эвтектику, отличающуюся низкой температурой плавления (988 °С) и располагающуюся по границам зерен. При горячей деформации границы зерен оплавляются, и сталь хрупко разрушается. От красноломкости сталь предохраняет марганец, который связывает серу в сульфиды MnS, исключающие образование легкоплавкой эвтектики. Устраняя красноломкость, сульфиды MnS, так же как и другие неметаллические включения (оксиды, нитриды и т. п.), служат концентраторами напряжений, снижают пластичность и вязкость стали. Содержание серы в стали строго ограничивают. Положительное влияние серы проявляется лишь в улучшении обрабатываемости резанием.
Фосфор - вредная примесь. Он растворяется в феррите, упрочняет его, но вызывает хладноломкость-снижение вязкости по мере понижения температуры. Сильное охрупчивающее действие фосфора выражается в повышении порога хладноломкости. Каждая 0,01 % Р повышает порог хладноломкости на 25 °С. Хрупкость стали, вызываемая фосфором, тем выше, чем больше в ней углерода. Фосфор - крайне нежелательная примесь в конструкционных сталях. Однако современные методы выплавки и переплавки не обеспечивают его полного удаления. Основной путь его снижения - повышение качества шихты.
Кислород, азот и водород - вредные скрытые примеси. Их влияние наиболее сильно проявляется в снижении пластичности и повышении склонности стали к хрупкому разрушению. Кислород и азот растворяются в феррите в ничтожно малом количестве и загрязняют сталь неметаллическими включениями (оксидами, нитридами). Кислородные включения вызывают красно- и хладноломкость, снижают прочность. Повышенное содержание азота вызывает деформационное старение. Атомы азота в холоднодеформированной стали скапливаются на дислокациях, образуя атмосферы Коттрелла, которые блокируют дислокации. Сталь упрочняется, становится малопластичной. Старение особенно нежелательно для листовой стали (≤0,1%С), предназначенной для холодной штамповки. Последствия старения-разрывы при штамповке или образование на поверхности полос скольжения, затрудняющих ее отделку.
Водород находится в твердом растворе или скапливается в порах и на дислокациях. Хрупкость, обусловленная водородом, проявляется тем резче, чем выше прочность материала и меньше его растворимость в кристаллической решетке. Наиболее сильное охрупчивание наблюдается в закаленных сталях с мартенситной структурой и отсутствует в аустенитных сталях. Повышенное содержание водорода в стали при ее выплавке может приводить к флокенам. Флокенами называют внутренние надрывы, образующиеся в результате высоких давлений, которые развивает водород, выделяющийся при охлаждении в поры вследствие понижения растворимости. Флокены в изломе имеют вид белых пятен, а на поверхности мелких трещин. Этот дефект обычно встречается в крупных поковках хромистых и хромоникелевых сталей. Для его предупреждения стали после горячей деформации медленно охлаждают или длительно выдерживают при температуре 250 °С. При этих условиях водород, имеющий большую скорость диффузии, не скапливается в порах, а удаляется из стали. Наводороживание и охрупчивание стали возможны при травлении в кислотах, нанесении гальванических покрытий и работе в водородсодержащих газовых средах.
Случайные примеси - элементы, попадающие в сталь из вторичного сырья или руд отдельных месторождений. Сталь, выплавленная из уральских руд, содержит медь, из керченских - мышьяк. Случайные примеси в большинстве случаев оказывают отрицательное влияние на вязкость и пластичность стали.
7. На какие свойства стали разного назначения влияет величина зерна?
Размер зерна влияет на свойства стали, особенно на вязкость, которая значительно выше у металлов с мелким зерном.
Внутри зерна феррита нет сильных препятствий скольжению. Поэтому сопротивление его деформации течения создают границы зерна, и чем мельче зерно феррита, тем выше предел текучести. Чем больше деформация, тем больше препятствий создают внутри зерна сами следы скольжения и тем меньше влияет размер зерна на сопротивление течению. Поэтому предел прочности σв зависит от размера зерна феррита слабее, чем предел текучести σт. Если потребитель использует сталь "в состоянии поставки", характеристикой стали может быть величина зерна феррита. Но если сталь будет термически обрабатываться, то важно "наследственное зерно аустенита", которое получится после нагрева под закалку до стандартной для этой стали температуры. У мартенсита столь сложная субзеренная структура, что в ней границы зерна исходного аустенита - препятствие пренебрежимо слабое. Прочность мартенсита от величины зерна не зависит. Перлит, сорбит, бейнит - двухфазные структуры. Их прочность определяется прежде всего температурой образования (дисперсностью цементита), а не величиной зерна исходного аустенита.
Мелкое зерно желательно при всех структурах, если есть риск хрупкого разрушения. Поэтому в высококачественных легированных конструкционных сталях наследственное зерно аустенита должно быть не крупнее 5-6-го балла.
8. Как управлять величиной зерна?
Величина зерен зависит от числа центров кристаллизации и скорости роста кристаллов. Чем больше центров кристаллизации, тем мельче зерно металла. Величина зерен, образующихся при кристаллизации, зависит от количества самопроизвольно зарождающихся центров кристаллизации и от количества нерастворимых примесей, всегда имеющихся в жидком металле.
Изменить число центров и размер зерна можно четырьмя методами:
- изменить скорость охлаждения и тем самым величину переохлаждения;
- увеличить или уменьшить перегрев металла перед разливкой;
- ввести в жидкий металл мельчайшие нерастворимые примеси;
- уменьшить путем добавки активных растворимых примесей поверхностное натяжение.
При небольшой степени переохлаждения (малой скорости охлаждения) будет получено крупное зерно. С увеличением степени переохлаждения размер зерна в затвердевшем металле уменьшается.
Последние два метода осуществляются при модификации введением специальных добавок. Ими являются оксиды (например, AI2O3), нитриды, сульфиды и другие соединения. Такие нерастворимые примеси являются готовыми центрами кристаллизации. Центрами кристаллизации в данном металле или сплаве могут быть только такие твердые частицы, которые по размеру соизмеримы с атомами основного металла. Кристаллическая решетка таких твердых частиц должна быть близка по своему строению и параметрам решетке кристаллизующегося металла. Чем больше таких частиц, тем мельче будут зерна закристаллизовавшегося металла. Чем выше скорость охлаждения, тем больше возникает центров кристаллизации и, следовательно, мельче зерно металла.
9. Что подразумевается под оптимальной структурой?
Основными компонентами, из которых состоят стали и чугуны, являются железо и углерод.
По структуре стали бывают:
- доэвтектоидные (феррит + перлит)
- эвтектоидные (перлит)
- заэвтектоидные (перлит + цементит)
Рисунок 1 Диаграмма состояния железо-цементит
Диаграмма состояния железо-цементит. Ж-жидкость; Ц-цементит (индексы: 1- первичный II-вторичный; III- третичный); А-аустенит; Ф-феррит; П-перлит (эвтектоид, т.е. механическая смесь феррита и цементита); Л-ледебурит (эвтектика, т.е. механическая смесь аустенита и цементита) Линия ACD - ликвидус, линия AECF - солидус. СD - линия первичного цементита (из жидкого расплава); SЕ- линия вторичного цементита (при перекристаллизации аустенита) РQ- линия третичного цементита (из феррит а).
10. Опишите процесс закалки стали
Закалка - термическая операция, состоящая в нагреве закаленного сплава выше температуры превращения с последующим достаточно быстрым охлаждением для получения структурно неустойчивого состояния сплава. Для сталей различают закалку до - и заэвтектоидных сталей. В структуре закаленной стали преобладает мартенсит. Мартенсит имеет высокую твердость и низкую вязкость, как конструкционный материал не используется. Для доэвтектоидных сталей температура закалки должна быть на 30 - 50 град. выше Ас3, а для заэвтектоидных - на 30 - 50 град. выше Ас1. При закалке доэвтектоидной стали с температуры выше Ас1, но ниже Ас3 в структуре наряду с мартенситом сохраняется часть феррита, который снижает твердость в закаленном состоянии и ухудшает механические свойства после отпуска. Такая закалка называется неполной. Для заэвтектоидных сталей оптимальная температура закалки лежит в интервале между Ас1 и Ас3 и теоретически является неполной. Здесь наряду с мартенситом закалки сохраняется часть оставшегося цементита, наличие которого полезно. Нагрев выше Ас3 приводит к вредным перегреву и обезуглероживанию стали. Закалка бывает объемной (под закалку нагревают насквозь все изделие) и поверхностной (осуществляют местный, чаще поверхностный нагрев).
В зависимости от формы изделия, марки стали и нужного комплекса свойств применяют различные способы охлаждения:
Закалка в одном охладителе. Нагретую до нужной температуры деталь переносят в охладитель и полностью охлаждают. В качестве охлаждающей среды используют: воду - для крупных изделий из углеродистых сталей; масло - для небольших деталей простой формы из углеродистых сталей и изделий из легированных сталей. Основной недостаток - значительные закалочные напряжения.
Закалка в двух средах или прерывистая. Нагретое изделие предварительно охлаждают в более резком охладителе (вода) до температуры ~ 300°С и затем переносят в более мягкий охладитель (масло). Прерывистая закалка обеспечивает максимальное приближение к оптимальному режиму охлаждения. Применяется в основном для закалки инструментов. Недостаток: сложность определения момента переноса изделия из одной среды в другую.
Ступенчатая закалка. Нагретое до требуемой температуры изделие помещают в охлаждающую среду, температура которой на 30 - 50°С выше точки МН и выдерживают в течении времени, необходимого для выравнивания температуры по всему сечению. Время изотермической выдержки не превышает периода устойчивости аустенита при заданной температуре. В качестве охлаждающей среды используют расплавленные соли или металлы. После изотермической выдержки деталь охлаждают с невысокой скоростью. Способ используется для мелких и средних изделий.
Изотермическая закалка. Отличается от ступенчатой закалки продолжительностью выдержки при температуре выше МН, в области промежуточного превращения. Изотермическая выдержка обеспечивает полное превращение переохлажденного аустенита в бейнит. При промежуточном превращении легированных сталей кроме бейнита в структуре сохраняется аустенит остаточный. Образовавшаяся структура характеризуется сочетанием высокой прочности, пластичности и вязкости. Вместе с этим снижается деформация из-за закалочных напряжений, уменьшаются и фазовые напряжения. В качестве охлаждающей среды используют расплавленные соли и щелочи.
Закалка с самоотпуском. Нагретые изделия помещают в охлаждающую среду и выдерживают до неполного охлаждения. После извлечения изделия, его поверхностные слои повторно нагреваются за счет внутренней теплоты до требуемой температуры, то есть осуществляется самоотпуск. Применяется для изделий, которые должны сочетать высокую твердость на поверхности и высокую вязкость в сердцевине (инструменты ударного действия: молотки, зубила).
11. Как управлять типом структуры, образующейся при закалке
Основными параметрами являются температура нагрева и скорость охлаждения.
По температуре нагрева различают виды закалки:
Полная, с температурой нагрева на 30…50°С выше критической температуры Ас3. Применяют ее для доэвтектоидных сталей. Изменения структуры стали при нагреве и охлаждении происходят по схеме: Неполная закалка доэвтектоидных сталей недопустима, так как в структуре остается мягкий феррит.
Неполная с температурой нагрева на 30…50 °С выше критической температуры Ас1. Применяется для заэвтектоидных сталей. Изменения структуры стали при нагреве и охлаждении происходят по схеме: После охлаждения в структуре остается вторичный цементит, который повышает твердость и износостойкость режущего инструмента. После полной закалки заэвтектоидных сталей получают дефектную структуру грубоигольчатого мартенсита. Заэвтектоидные стали перед закалкой обязательно подвергают отжигу - сфероидизации, чтобы цементит имел зернистую форму.
Охлаждение при закалке.
Для получения требуемой структуры изделия охлаждают с различной скоростью, которая в большой степени определяется охлаждающей средой, формой изделия и теплопроводностью стали.
Режим охлаждения должен обеспечить необходимую глубину закаленного слоя. При высоких скоростях охлаждения при закалке возникают внутренние напряжения, которые могут привести к короблению и растрескиванию.
Очень медленное охлаждение может привести к частичному отпуску мартенсита и увеличению количества аустенита остаточного, а следовательно к снижению твердости.
В качестве охлаждающих сред при закалке используют воду при различных температурах, технические масла, растворы солей и щелочей, расплавленные металлы.
12. Опишите понятия "закаливаемость" и "прокаливаемость"
Закаливаемость и прокаливаемость - важнейшие характеристики сталей.
Закаливаемость - способность стали приобретать высокую твердость при закалке.
Закаливаемость определяется твердостью поверхности закаленной детали и зависит главным образом от содержания углерода в стали. При закалке, различных деталей поверхность их, как правило, охлаждается со скоростью, большей VКр, следовательно, на поверхности образуется мартенсит, обладающий высокой твердостью. Стали с содержанием углерода менее 0,2% не закаливаются.
При закалке любых деталей даже в самых сильных охладителях невозможно добиться одинаковой скорости охлаждения поверхности и сердцевины детали. Следовательно, если скорость охлаждения сердцевины при закалке будет меньше VKp, то деталь не прокалится насквозь, т. е. там не образуется мартенсит.
Прокаливаемостью - называют способность стали закаливаться на определенную глубину.
Условились при оценке прокаливаемости закаленными считать слои, в которых содержится не менее 50% мартенсита (полумартенситная зона).
Установлено, что легирование стали любыми элементами, кроме кобальта, увеличивает прокаливаемость, так как при этом повышается устойчивость переохлажденного аустенита.
13. Что такое "полоса прокаливаемости"? Дайте описание "полосы прокаливаемости" стали, заданной номером рисунка в варианте задания
Прокаливаемость - способность получать закаленный слой с мартенситной и троостомартенситной структурой, обладающей высокой твердостью, на определенную глубину. За глубину закаленной зоны принимают расстояние от поверхности до середины слоя, где в структуре одинаковые объемы мартенсита и троостита. С введением в сталь легирующих элементов (Сr, Ni, Мо, Мn, W, V) закаливаемость и прокаливаемость увеличиваются.
Таблица 2 Полосы прокаливаемости стали 38ХС
14. Что такое стали пониженной прокаливаемости, и для каких деталей их применяют?
Под прокаливаемостью подразумевают глубину проникновения закаленной зоны. Несквозная прокаливаемость связана с тем, что деталь быстрее охлаждается с поверхности, чем с сердцевины. С уменьшением критической скорости закалки увеличивается и глубина закаленного слоя, и если Vк будет меньше скорости охлаждения в центре, то сечение закалится на сквозь. Если сечение велико и скорость на поверхности меньше Vк, то сталь не закалится даже на поверхности. Для практической оценки прокаливаемости используют величину - критический диаметр, т.е. максимальный диаметр (размер) образца, который прокаливается насквозь в данном охладителе. Чем лучше свойства охладителя тем больше Dкр.
Для получения при закалке тонкого твердого слоя, равномерного по поверхности применяют мелкозернистые стали с пониженной прокаливаемостью, у которых ограничено содержание марганца и кремния, а также хрома, никеля, меди и пр. и создана устойчивая наследственная мелкозернистость путем модифицирования алюминием, титаном и пр. При увеличении содержания алюминия (сверх 0,10-0,12%) измельчение зерна прекращается, но так как твердый раствор продолжает обогащаться алюминием, прокаливаемость стали повышается.
Например:
В автомобильной промышленности для шестерен неответственного назначения, допускающих сквозную закалку зубьев (например, венец маховика автомобильных двигателей, работающий только при пуске), используют сталь с пониженной прокаливаемостью марки 55ПП содержащей 0,55 - 0,63%С и <0,5 % примесей (Si, Мn, Сr и Си) и регламентированной прокаливаемости 47РП, содержащей 0,44 - 0,51%С; 1,0 - 1,2 % Мn; 0,06 - 0,12%Тi.
15. Опишите процесс старения стали
Старение - термическая обработка, при которой главным процессом является распад пересыщенного твердого раствора.
В результате старения происходит изменение свойств закаленных сплавов.
В отличие от отпуска, после старения увеличиваются прочность и твердость, и уменьшается пластичность.
Старение сплавов связано с переменной растворимостью избыточной фазы, а упрочнение при старении происходит в результате дисперсионных выделений при распаде пересыщенного твердого раствора и возникающих при этом внутренних напряжений.
Основное назначение старения - повышение прочности и стабилизация свойств.
Различают старение естественное, искусственное и после пластической деформации.
После старения повышается прочность и снижается пластичность низкоуглеродистых сталей в результате дисперсных выделений в феррите цементита третичного и нитридов.
16. Перечислите требования к автомобильному листу
Основную массу производимого холоднокатаного листа составляет автомобильный лист. Кузов автомобиля изготовлен холодной штамповкой (и точечной сваркой) из тонкого (0,5...3мм) листа. Листовым сталям необходим высокий запас технологической пластичности (способности металла подвергаться горячей и холодной пластической деформации).
Технологическая пластичность зависит от химического состава стали, ее микроструктуры и контролируется параметрами механических свойств. Способность стали к вытяжке при холодной штамповке определяется концентрацией углерода. Чем она меньше, тем легче идет технологический процесс вытяжки. Для глубокой вытяжки содержание углерода в стали ограничивают 0,1%; при 0,2-0,3%С возможны только гибка и незначительная вытяжка.
Микроструктура стали должна состоять из феррита с небольшим количеством перлита. Выделение по границам зерен структурно свободного (третичного) цементита строго ограничивается во избежание разрывов при штамповке. Лучше всего деформируется сталь с мелким зерном, соответствующим 7-8 номеру по ГОСТ 5639-82. При большем размере зерна получается шероховатая поверхность в виде так называемой апельсиновой корки, при меньшем - сталь становится слишком жесткой и упругой. Также нежелательна разнозернистая структура, поскольку она способствует неравномерности деформации и образованию трещин.
Для глубокой, сложной и особосложной вытяжки используют малопрочные (σв = 280-ЗЗО МПа), высокопластичные (δ = 33-45 %) стали 05, 08, 10 всех видов раскисления. Их поставляют в виде тонкого холоднокатаного листа, подвергнутого рекристаллизационному отжигу при температуре 650-690 °С. Широко применяют кипящие стали 05кп, 08кп и 10кп. Для глубокой вытяжки чаще всего используют сталь 08кп.
Кипящая сталь из-за повышенной газонасыщенности склонна к деформационному старению. В связи с этим для холодной штамповки используют сталь, микролегированную ванадием 08Фкп (0,02-0,04%V) или алюминием 08Юкп. Ванадий и алюминий связывают примеси внедрения (азот, кислород) в прочные химические соединения и препятствуют развитию деформационного старения.
Применяются также полуспокойные и спокойные стали 08пс и 08, которые, несмотря на меньшую пластичность, обладают более высокой стабильностью свойств.
17. Как понимать термин хорошая "свариваемость стали"?
Свариваемость - способность получения сварного соединения, равнопрочного с основным металлом. Для образования качественного соединения важно предупредить возникновение в сварном шве различных дефектов: пор, непроваров и, главным образом, трещин. Характеристикой свариваемости данного металла служат количество допускаемых способов сварки и простота ее технологии.
Свариваемость стали тем выше, чем меньше в ней углерода и легирующих элементов. Влияние углерода является определяющим. Углерод расширяет интервал кристаллизации и увеличивает склонность к образованию горячих трещин, которая тем больше, чем дольше металл шва находится в жидком состоянии.
В связи с этим высокой свариваемостью обладают стали, содержащие до 0,25% С. К ним относятся углеродистые стали (БСт0, БСт1-БСт4, ВСт1-ВСт4; 0,5, 08, 10, 15, 20, 25), а также низколегированные, применяемые для изготовления различных металлоконструкций: стали для трубопроводов, мостостроения, вагоностроения, судостроения 09Г2(Д), 09Г2С, 14Г2, 15ГФ(Д), 16ГС, 17ГС и др.; стали с карбонитридным упрочнением, применяемые для мостов, металлоконструкций цехов, кранов, резервуаров 14Г2АФ(Д), 15Г2СФ(Д), 16Г2АФ и др.
Сварка всех этих сталей при толщинах до 15 мм не вызывает затруднений. Сварка таких же сталей больших толщин и в термически упрочненном состоянии требует подогрева и термической обработки.
При сварке углеродистых и низколегированных сталей, содержащих более 0,3%С, возникают затруднения из-за возможности закалки и охрупчивания околошовной зоны.
Сварка высокохромистых и хромоникелевых сталей в связи с неизбежными фазовыми превращениями в металле требует специальных технологических приемов - снижения скорости охлаждения, применения защитных атмосфер и последующей термической обработки.
18. От чего зависит контактная прочность стали?
Для того чтобы обеспечить работоспособность конкретных машин и приборов, конструкционный материал должен иметь высокую конструкционную прочность.
Конструкционной прочностью называется комплекс механических свойств, обеспечивающих надежную и длительную работу материала в условиях эксплуатации.
Требуемые характеристики механических свойств материала для конкретного изделия зависят не только от силовых факторов, но и воздействия на него рабочей среды и температуры.
Высокая прочность и долговечность конструкций при минимальной массе и наибольшей надежности достигаются технологическими, металлургическими и конструкторскими методами.
Наибольшую эффективность имеют технологические и металлургические методы, цель которых - повышение механических свойств и качества материала.
Прочность - свойство, зависящее от энергии межатомной связи, структуры и химического состава материала. Энергия межатомного взаимодействия непосредственно определяет характеристики упругих свойств (модули нормальной упругости и сдвига), а также так называемую теоретическую прочность.
Проблема повышения конструкционной прочности состоит не столько в повышении прочностных свойств, сколько в том, как при высокой прочности обеспечить высокое сопротивление вязкому разрушению, т. е. надежность материала.
В углеродистых сталях закалкой на мартенсит и низким отпуском можно получить при содержании 0,4%С σв≈2400 МПа, при 0,6%С σв≈2800 МПа. Однако при такой прочности стали хрупки, эксплуатационно ненадежны.
Заданные прочность, надежность, долговечность достигаются формированием определенного структурного состояния.
Формированию благоприятной структуры и обеспечению надежности способствуют рациональное легирование, измельчение зерна, повышение металлургического качества.
19. Назовите уровни прочности канатной стали и опишите технологию упрочнения
Канатную проволоку свивают в канаты (для судов, шахт, лифтов, кранов). При диаметре 1 мм и менее стандарты разных стран гарантируют для канатной проволоки предел прочности σв > 1300...2400 МПа.
При такой прочности проволоке нужен и запас пластичности: нити каната должны выдерживать перегибы и удары. Этот запас проверяется испытаниями: на многократный "гиб с перегибом", скручивание, навивку, разрыв с узлом. Необходимая структура - тонкопластинчатый перлит (сорбит), упрочняемый холодным волочением. Чтобы выдерживать при этом большие обжатия, нужна эвтектоидная сталь - углеродистая сталь 65...85.
Чем тоньше пластинки цементита в перлите, тем больше упрочнение. Пластинки тем тоньше, чем ниже температура распада переохлажденного аустенита. Оптимальную температуру изотермического распада надо быстро достичь (если распад начнется выше, перлит грубее) и точно выдержать (чуть ниже появятся менее пластичные игольчатые структуры - бейнит). Поэтому делается патентирование: протягиваемая проволока проходит через печь (или соляную ванну) нагрева и быстро охлаждается до температуры распада аустенита в ванне с расплавом свинца или солей. После волочения делается еще низкий отпуск для снятия напряжений.
К стали для патентирования есть ряд жестких требований
Во-первых, чистота по легирующим элементам (Сг < 0,10%; Ni < 0,15%; Сu < 0,2%), иначе изотермический распад аустенита за время пребывания в свинцовой ванне не закончится, а остаток аустенита на выходе из ванны даст хрупкий мартенсит или бейнит. Использование лома в шихте исключается.
Во-вторых, вытягиваясь при волочении, границы зерна исходного аустенита превращаются в ленты вдоль оси проволоки. Если на них были сегрегации фосфора или наночастицы AlN или MnS, проволока расслаивается по этим лентам при скручивании (или при волочении). Поэтому когда-то сталь для пружин плавили только из древесноугольного чугуна (чистого по фосфору и сере). Сегодня его заменило железо прямого восстановления.
В-третьих, важна чистота по неметаллическим включениям. Если включения деформируемы и при холодном волочении (как MnS), то из округлых в слитке они превратятся в нити макроскопической длины и субмикронной толщины, а включения - дендриты - в пучок нитей, по которым и произойдет расслой. Канаты из стали 60 с округлыми сульфидами (от введения РЗМ) выдерживали 25000 перегибов, а с длинными включениями - только 18000.
20. Назовите виды коррозионных повреждений нержавеющей стали
Коррозией - называется разрушение металлов и сплавов вследствие химического и физико-химического воздействия на них окружающей среды. При техническом проектировании серьезное внимание уделяется мероприятиям защиты от коррозии.
Различают два вида коррозии металлов: химическую и электрохимическую.
Химическая коррозия происходит при воздействии на металл или сплав сухих газов при повышенных температурах и жидких неэлектролитов (бензин, смола, масло и др.).
или зарегистрироваться
в сервисе
удобным
способом
вы получите ссылку
на скачивание
к нам за прошлый год